Copyright
© 2002-2017 John Mayer. All rights reserved.
For reuse policy see Reuse Policy
In this Section:
(note: press the Home key to return to the Section
Contents)
Oven Replacement
After
many years as fulltime RVers we found that we never used the gas oven.
We have always had a convection microwave, and we use that for all our
cooking and baking needs. The gas oven was used for storage of pots,
pans, and bread. So we decided to replace the range with a cook top, and
turn the gas oven space into drawers. It was a relatively simple job if
you are handy with woodworking. The biggest issue for us was matching
the drawer edges to the rest of the RV. That proved to be impossible
without having custom router bits made (at a cost of over $200). Even
Carriage, the maker of our 5th wheel, would not make drawer fronts for
us. Unfortunately, they use a custom edge and we can not find any router
bits (or combinations) close enough to match theirs. This would not be
an issue with almost any other manufacturer.
To overcome this "issue", we decided to make
recessed drawers, and then cover them with a piece of black Lexan or
plexiglass. The black would hide the drawers, and match the black cook
top - it almost appears as if an oven is still there.
We had a piece of custom-cut black plexiglass made
for us. You could use clear plexi - available at Home Depot or Lowes -
and spray it black. But it would not look as good as the black plexi. We
decided not to use Lexan because of the cost (it was three times as much
as plexiglass) and the fact that the door should not get that much
abuse. Lexan will scratch less than plexiglass, though, and if it proves
to be an issue we may have to replace the door in the future with Lexan.
The original range was easily removed and disposed
of. The replacement cook top was the same brand, obtained at the local
Camping World. It dropped into the counter opening perfectly. A new
stile was made to frame under it. The two drawers are made of
conventional birch plywood construction, with full-extension 100-pound
drawer slides. They are faced with oak and stained to match the rest of
the cabinets. They are recessed about an inch from the front stiles of
the cabinet when closed.
The plexi was mounted to the face of the cabinet -
it overlaps a little on all sides of the opening. The hinges are the
type that go around the plexiglass and secure with a set-screw. This is
convention "glass" hinging with no holes in the plexiglass. A
"pop-magnet" is used to secure the door closed. To open it you simply
press in on the glass and it pops open.
Click on the pictures to expand them.
Back to Page Contents (top)
Fire
Suppression
The presentation I did on Fire Safety at
the 2011 HDT Rally is
here.
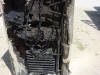 We
have always been aware of the danger of fire in the confined space of an
RV. We carry several foam and dry chemical extinguishers with us, and
they are placed in appropriately convenient areas around our RV. You
need several of these extinguishers, since an extinguisher that is not
close at hand is pretty worthless. You do not want to be in the position
of having fire between you and your extinguisher! Shown to the left is
the result of a simple refrigerator fire. This fire happened while the
owners were at home, and they were able to suppress it enough with
extinguishers until the fire department could get there. They were
"lucky" - if they had been away, or if it had happened while they were
asleep the result probably would have been a totally consumed coach.
Instead, there was $100,000 worth of damage.
Most fires in RVs are either in
the engine compartment, generator compartment, wheels/tires or refrigerator.
Engine fires account for the majority of fires. What would you do if you
had an engine fire in your RV? In most RVs the engine is pretty well
enclosed, and it is difficult to get to for fire fighting. Your ability
to get to the source of the fire has everything to do with the
probability of extinguishing it (even assuming you are present).
Automated, temperature activated
fire suppression systems are now available at relatively moderate
prices. These generally use Halon (or its replacement products), or
water-based foam/surfactants. Manufacture of Halon has been outlawed
because of environmental considerations, but it is still available. DuPont
FE-36 is one of the popular Halon replacements, and is about as
effective. All of these options have excellent fire suppression
capabilities, pretty good re-ignition and flashover suppression, and no
cleanup issues. They are far superior to dry chemical and CO2. Water is
better than nothing, but is not considered a reasonable fire suppression
product.
Foam (referred to as AFFF –
aqueous film forming foam) is really effective on class B fires, but can
be highly toxic and pretty hard to clean up, depending on its
formulation.
Water-based surfactants are very
effective on class A and B fires. They are now widely used in racing,
are non-toxic, and biodegradable. There are several trade names that you
will see advertised: FireX, FireAde and Cold Fire are a few. They work
by absorbing huge quantities of heat, act as a dispersal agent, and
suppress vapor release. They are by far the best extinguisher for fires
like tires and engines. Extinguishers using surfactants can also be
maintained easily by the owner, since they are water-based with a
chemical powder added.
Both
Halon and surfactant extinguishers are available in permanently mounted,
automatic/manual-deployed systems, and in hand-held extinguishers. You
should consider both, in my opinion. Any RV engine compartment should
have an automatically-deployed surfactant or Halon suppression system.
You can supplement that with hand-held extinguishers, but the advantage
of a temperature or remotely activated system is that it is already at
the fire source (you do not have to open hoods, etc). Expect to spend
from $400-$2500 for an engine compartment/generator compartment complete
suppression system. The other place to consider extinguishers is in the
generator compartment, and refrigerator compartment. You can get
“all-in-one” automated Halon or Cold Fire extinguishers that work well
in the refrigerator or generator compartment for as little as $125.
Shown at the left is the automatic Halon extinguisher we purchased for
our refrigerator compartment.
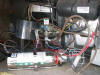 There
are quite a few refrigerator fires in RVs. No statistics are available,
but we personally know four people who have had fires, and have heard of
many, many others. In our opinion, adding an auto extinguisher to the
refrigerator compartment is “cheap” insurance. In our case we added a
one pound Halon extinguisher to our refrigerator compartment that
automatically deploys at 165 degrees. We obtained this from Fire
Fight, a manufacturer of high performance fire suppression
systems. We consider it well worth the $125 that it cost us. The second
picture is the same extinguisher in another refrigerator compartment.
Note: due to the owners death, Fire Fight is having issues shipping
product. Because of this, I can no longer recommend them as a source.
The business is in the process of being relaunched by new owners as
Fire Fight Products, so you might want to check that website and do
a search on the web to ensure they are shipping product. Or, just call
them. In the meantime, I would check with Mac McCoy for a system.
We recently met a couple who had
lost a towed vehicle due to a tire fire. Fortunately, they were able to
unhook it from their coach and pull the coach away - many are not so
fortunate and lose the coach as well as the car. One thing they told us
of note was that once the tire rubber started burning their dry chemical
extinguishers had basically no effect on the fire. Only a
surfactant-type of extinguisher like Cold Fire would have had a chance
at suppressing a tire fire. This tire fire was caused by a blowout on
the front/left tire. Would you know if you had a blow-out on your towed
vehicle? Before it caught fire? Take a look at the tire monitor section
of this website for some options on tire management.
Cold Fire handheld extinguishers
and automated systems based on Cold Fire are available from
RV Safety Systems. The engine compartment “systems” they offer are
truly that – a complete system that can monitor and protect BOTH the
engine compartment and generator compartment. They are not particularly
cheap, but considering the alternative I think they are worth
considering if you have a motor home. Also, you may receive an
insurance company discount if a suppression system is installed.
Probably the best source for
both Cold Fire and FireAde hand held products (including
auto-suppression systems) is
Mac McCoy (also known a “Mac the Fire Guy”).
Back to Page Contents (top)
Blu Dot
Air-Over-Hydraulic Brake System
The presentation on BluDot from the 2011 HDT Rally is
here.
Brake controllers and braking systems for trailers
are a subject of great debate among experienced and "techie" trailer
owners. If you own a heavy 5th wheel you may of encountered a situation
where you wish you would have had more effective brakes. There are
several components of the braking system that can be improved,
including:
-
The brake controller
(pendulum type, direct connect proportional systems, integrated
systems)
-
The actuation system (the
system that "translates" the brake signal into the brake itself)
-
The type of brake on the
trailer (disc or drum)
Note: click on all thumbnails
to expand to full size.
In
this section we will consider the Blu Dot air over hydraulic brake
system. This system is used with tow vehicles that have air brakes and
are towing RV's with hydraulic disc brakes. It fully integrates the
trailer braking system into the truck airbrake system, in much the same
way that a tractor is integrated into the semi-trailer system. The
advantages of the Blu Dot system are that there is no controller on the
truck needed to "translate" an electric brake signal into a hydraulic
signal, and that all the truck components operate in their normal
fashion with no modifications. Even the hand-brake (Johnson bar) on the
dash works just like with a semi-trailer. The only signal translation
that takes place in this braking system is at the actuator, where the
air signal (service line proportional pressure) is translated to
hydraulic pressure in the master cylinder. As contrasted to the several
other methods of actuating hydraulic disc brakes this has the advantage
that there is no translation of original signal from the pickup point on
the truck (either the airline tap, or the brake line electrical tap)
through a controller of some sort to an electric signal. Typically this
electric signal originating from the controller is then sent through an
electrical line in the truck to a connector, then through another
connector on the trailer to the hydraulic actuator where it is again
translated into hydraulic pressure. There are several issues with this
process. First, the original "tap" of the signal on the truck may not be
accurate and can be prone to failure. Second, the connectors crossing to
the RV are notorious for having issues and signal loss. Third, braking
action is dependent on the quality of the electrical signal and fourth,
multiple translations of signal at various points in the process can
lead to problems.
The Blu Dot actuation system
circumvents all these issues by using the normal tractor gladhands and
trailer connectors for braking. The tractor is designed with this in
mind, and has many proven failsafe mechanisms to manage the quality of
braking. The only translation of signal occurs at the endpoint - the
brake actuator itself - where the airline pressure coming from the
service line on the tractor is use to proportionately drive the master
cylinder. No electric lines are used at all in the braking process, thus
the biggest flaw of the other systems is totally avoided.
To
install the Blu Dot system you must have an intact tractor protection
valve on your truck. The tractor protection valve is on the rear of the
truck cab (typically) and has the coiled airlines connected to it. One
airline is blue - this is the "service line". The other airline is red -
this is the "emergency" airline. The emergency airline supplies air to
the brake system on the trailer. The air is stored in a tank on the
trailer and then used as required to operate the trailer brakes. On a
semi-trailer with airbrakes it operates the brakes identically to the
way the regular tractor airbrake operates- there is no real difference
between the brakes on a semi-trailer and on the tractor itself.
On an RV with hydraulic disc
brakes there is still a tank, and that tank supplies the air that is
used to drive the master cylinder. The service line (blue line) is a
signal line. When you step on the service brakes in the truck, air is
sent out the service line in proportion to how hard you press the brakes
(a simplified explanation). Many times the emergency and
service lines exiting the tractor protection valve are capped for RV
use. You need to tap these exit points on the valve. Typically, you
would run airline from each of these exits to the back of the tractor
and install gladhands at some appropriate location. The first picture to
the left shows a tractor protection valve with the output ports capped.
In the installation on this truck this valve needed relocation, since
there was not enough clearance between the hauler body and the valve for
airlines to exit.

To the left you can see where
the airlines are extended to on my truck. Gladhands were added to
connect the coiled airlines to. Blue is the service line, red the
emergency. If you are familiar with semitrailers then you might wonder
why the gladhand ends are on the truck, and NOT on the trailer where
they "belong". The reason is that in RV use the truck is dedicated to a
single trailer and it is more convenient to just keep the airlines with
the trailer. It could be either way; functionally, it makes no
difference. If the trailer ever needed to be moved with a different
truck with airlines on the truck side, you can simply interconnect the
lines. On my truck I put the gladhand ends on each side of the tunnel.
The purpose was to help keep the airlines from tangling. This works
well, but you can put them right next to each other as well - that would
be the more conventional placement. Note that on the emergency (red)
gladhand there is a dummy connector with a quick-connect airline fitting
on it. This allows me to use the tractor air system as a source for air
tools or for filling tires. Simply plug in an airline like you would on
a compressor. When attaching the air coils for operation of the braking
system this dummy connector is removed and stored.
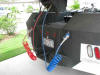
Here
you can see the airline coils coming out of the hitch area on the
trailer. In retrofit installations the hardest part of the job may be to
run the airlines through the gooseneck portion of the trailer from the
main storage compartment. In some cases, this may not be possible
because of cross framing in the gooseneck. In that case, the airline
coils can be terminated through the main compartment wall, and simply
stretched across to the trailer when hooked up. Each implementation will
be a little different. The close-up of the hitch head shows how the
bulkhead fittings are attached to the hitch head. Again, each
implementation may be a little different. In this case I bolted on a
piece of aluminum flat to tie the bulkhead fittings to.
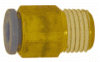 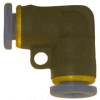
When installing and working with airlines on the
truck you will likely need to purchase connectors. The Blu Dot kits come
with most everything you need for the trailer-side. But you will need
some parts for the truck side and to customize the trailer end of
things. A wide variety of connectors is available online at
http://fittingsandadapters.com/. They have good prices and prompt
delivery. You can also purchase airline connectors at truck service
departments and many auto-parts stores. But you will pay more, in most
cases.
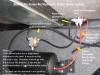
To the left you can see the major components that you
have to locate in the trailer. In particular, the tank and control
valves. These can be located anywhere, even underneath the trailer. The
control valve attached to the tank must be placed in one of the large
ports on the tank, but other than that, the tank can be oriented in any
direction, even vertically. Just make sure the control valve is not on
the bottom of the tank. The reason for this restriction is that if it
was, it could pick up any water that condenses in the tank. You also
need to have a drain line/pressure relief line on the bottom someplace.
This will drain any accumulated water from the tank, and
to also relieve the tank pressure when you disconnect the truck.
Why do this? The way the BluDot is designed, if the emergency line loses
pressure - like would happen in a trailer breakaway situation - then the
valve that you see in the picture on the ceiling of the storage
compartment will divert air from the tank to the actuator. This causes
the trailer brakes to lock-up, stopping the trailer immediately. When
you disconnect the red aircoil from the truck at your campsite this has
the same effect as a disconnect - the trailer brakes lock. While this is
convenient to keep the trailer from moving while setting up, it is not
good to leave pressure on the disc brakes for long periods of time. It
is not good for the seals, and the brakes can lock in that position. So
there must be a way to dump the air from the tank once you are setup in
camp.
The general purpose of the
relay valve (the control valve) is to function as a
remote-controlled brake valve to speed up both the application and
release of the service brakes on tractors and trailers. In this case the
valve is in the trailer. The valve relays a small volume of modulated
signal pressure from the control valve into a large volume of
modulated delivery air from the service reservoir (air tank) of similar
pressure to the service brake chamber (brake can) attached to the master
cylinder (this is the BluDot proprietary "joined" master cylinder/brake
can). So, the valve takes an input from the truck, and pulls air from
the tank at around the same pressure and sends it to the actuator (the
brake can/master cylinder).
With a control port, supply
port, delivery port and an exhaust port, when the control valve
is operated, the relay delivers air from the service reservoir to the
brake can at the same pressure as the control signal, causing the brakes
to apply. As long as the control pressure is maintained, the relay will
hold a like pressure in the air chamber and automatically replace any
air lost because of minor leaks between it and the air chamber (brake
can).
Releasing the control valve
pressure signals the relay to exhaust the air from the chambers through
the relay exhaust port. If control pressure is partially released, then
the service brake pressure will be released proportionately. This is
important - it is the only way pressure is relieved from the master
cylinder/brake can assembly.
This relay valve
assembly is the part that sits on top of the air tank (service
reservoir) and it has four output delivery ports.
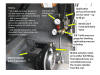
Shown here is the actuator, which consists of a truck
brake can integrated with a master cylinder. In the case of Kodiak
brakes a Bendix LQ-4 front axle brake valve is recommended
by Kodiak and BluDot to ensure
line pressures do not normally exceed 90psi. Kodiak has had some issues with high hydraulic line pressure damaging their brakes. Using this
valve is intended to ensure that in normal operation more than 1000psi is never seen
in the brake lines. The LQ-4 valve is not ideally suited for this
application because it eliminates braking on the trailer
until 20 psi is reached, and then it limits braking. Once the equalization pressure point (70psi) is reached, which then
allows all air to pass. This has the unwanted effect of reducing trailer
braking in mild-to-low braking situations. A panic stop with hard
application would cause more than 70 psi pressure and trigger the "pass
thru" so you would get full braking. Remember that normal to
hard braking on a tractor is using 15-30 psi at the application side.
A
Bendix RV-1
reducing valve (102196, 90 psi reducing valve) installed between
the emergency valve and the tank is a superior solution to the LQ-4
valve. The
reducing valve plumbed into this location will only allow the tank to be
pressured to 90 psi. Thus, no more than 90 psi will ever reach the brake
can on application. This will meet the pressure requirements of the
Kodiak brakes without reducing braking function in the mild-to-low
braking situation. Putting the valve in this location will not restrict
flow to the master cylinder/brake can. My advice is to NOT put in the
LQ-4 and to instead put in the RV-1. This has been successfully tested
in the field and operates as noted here. But it is up to you - and I
can't take responsibility for your decisions, one way or another. If it
was my rig I'd put on the RV-1, though.
With Dexter disc brakes this component would not be
used, and the airline would directly connect to the brake can. Note the
air pressure gauges. One is in the drain/relief line. This shows the
tank pressure under normal operating conditions. The gauge in the
service line going into the brake can shows the application pressure.
Both are optional, but make testing and debugging the system much
simpler. The gauge with the T are under $15 - in my opinion it is money
worth spending. Especially on the drain line - since forgetting to drain
the tank for long periods when the trailer is unhooked can have a
serious impact on the brakes.
Some more pictures are on my Picasa album
here.
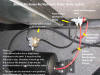
Back to Page Contents (top)
Converting to an LCD TV
In
our Royals International we converted the entertainment center from
housing a 24" Sony tube TV to a 32" Samsung LCD TV. I mounted this on a
custom made swing-away mounting system in order to utilize the space
behind the TV. The TV sat on the "face" of the cabinet, since the newer
16:9 ratio LCD was wider than the previous 4:3 ratio TV. This is a
typical issue you will face when upgrading a tube TV to an LCD. Some
variant of the techniques I used should work for most installations.
The story is best told in pictures. Check out my Picasa album
TV Mount. |